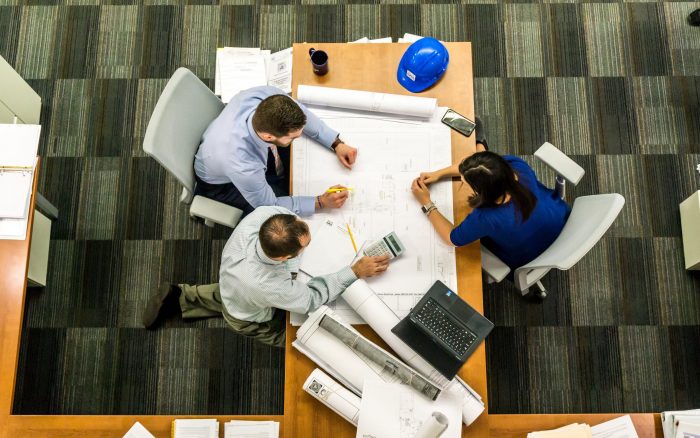
HOW CAN YOUR COMPANY ANALYZE THE ROI OF SAFETY?
As a business owner, the safety and health of your employees is your number one priority. This is not only a requirement by law, but one of moral obligation, where you recognize the value in your workers as individuals and respect their right to a safe and healthful workplace. The dilemma comes from how you meet this requirement and survive the impact it can have on your bottom line. Implementing safety programs and training can be very costly, made more frustrating by the fact that results aren’t immediately visible and can be difficult to quantify. Determining the long-term cost savings of incorporating an all-encompassing safety culture is often referred to as ROI, or Return on Investment.
OSHA, COSTS, AND ROI
According to the Occupational Safety and Health Administration (OSHA), businesses see an average return of $4 to $6 for every dollar invested into their workplace safety programs. To get an idea of how ROI works, it’s important to start by inspecting the actual cost of an injury.
OSHA estimates that businesses in the U.S. lose nearly $2 billion each year as a result of worker injury and harm to health. Shockingly, this number reflects only direct costs such as workers’ compensation, liability and litigation costs, loss of property, fines, and medical expenses. Chances are the indirect costs are much higher. Indirect costs include retraining, increased insurance premiums, attorney’s fees, lost time, worker replacement, and loss in productivity. According to the Center for Disease Control (CDC), indirect costs add up to $2.12 for every dollar lost in direct costs, bringing their estimate for the cost of a fatal workplace injury from $1.4 million to nearly $3 million.
OSHA provides a formula to estimate indirect costs of an injury based on national averages:
Direct Cost x Cost Multiplier = Indirect Cost

This says nothing of the sales required to compensate for the costs over time. Look at the following example:
For a single burn injury, the direct costs average $37,389 and the indirect costs average $41,127 for a total cost of $78,516. It will require a company with a 3% profit margin $1,370,930 in sales before the indirect costs alone are covered, and $2,617,200 in sales to cover the total costs.
It’s easy to see how quickly and profoundly the impact of a workplace injury can add up when you take hidden, indirect costs into consideration.
QUANTIFYING ROI
Costs can come in any number of combinations, which is what makes actually quantifying a return on investment so difficult. When you deliver safety training, the only benefit you see right away is simply that the worker does not receive an injury due to their increased procedural knowledge. There’s nothing to measure besides costs from an injury that’s only hypothetical. You have to look at safety ROI in the same way you look at something like automobile insurance – you pay for it now so you don’t pay more later.
In an ideal world, you meet the ultimate safety goal of 0 incidents, 0 injuries, and 0 illnesses. This should be your ultimate target when designing and implementing your workplace safety program. However, almost 50 workers are injured every minute of the workweek and 17 die each day, according to OSHA. Many of these incidents can be attributed to the fact that almost half of the 95 million workers who should be covered by an OSHA-approved workplace safety program aren’t properly so. Skipping steps and letting startup investments deter you from protecting your workers both puts them in danger and opens the door to the great possibility of incident. The Voluntary Protection Program who partners with OSHA reports that over 500 workplaces among 180 industries see savings over nearly $110 million each year because their injury rates are 50% below average for their respective industries.
Investment returns aren’t always as measurable as end-of-year numbers. Returns can also come in the form of increased morale. Businesses that provide thorough workplace safety programs end up with an environment which allows employees to feel safe when they clock in. A sense of safety and security translates to workers who can concentrate on their jobs rather than the proverbial ax hanging over their heads. This leads to both increased loyalty and a stronger image for your business where future quality potential applicants are concerned. A stronger business image will also improve your reputation in terms of attracting repeat sales, customers, investors, and suppliers.
HOW TO INVEST IN SAFETY?
How you decide to invest in safety will depend greatly on your individual workplace. Your industry, number of employees, equipment used, and state and federal laws will impact your purchasing decisions, but a total examination of your workplace starting with a Job Hazard Analysis (JHA) is a good place to start. A JHA entails surveying the landscape of your workplace to identify known or potential safety hazards, and then using those results to determine an effective course of action for neutralizing or displacing those hazards, including what training is necessary.
Many companies today are finding that centralizing training in a Learning Management System (LMS) is an extremely cost-effective method of administering training to multiple employees with customizable courses and progress tracking features. Using an LMS removes the need to contract professional trainers, reduces loss of productivity that comes with scheduled classroom training, and improves safety management efficiency by giving administrators access to training progress and reporting features. Using these features allows employers to identify additional training needs and zone in on specific weak spots, all in a single convenient location, opening space in their personnel roster that would otherwise be spent on a safety team for a more complicated program.
FAST AND AFFORDABLE SOLUTIONS
Safety Services Company offers custom training solutions for employers across numerous industries so they can see for themselves what ROI of safety looks like. Whether your current safety program needs a fresh update, you’re ready to implement a new one, or you want to explore the convenience and cost savings of an LMS, we can help you meet compliance.
Need more help? To learn more about how we can solve your company’s safety training and compliance needs, check out our resources here or call us at (866) 329-5407 today. Remember, your one call could save lives and improve your company’s ROI.