Episode 13: Management Systems in Environmental Health & Safety
January 5th 2022
- Undefined
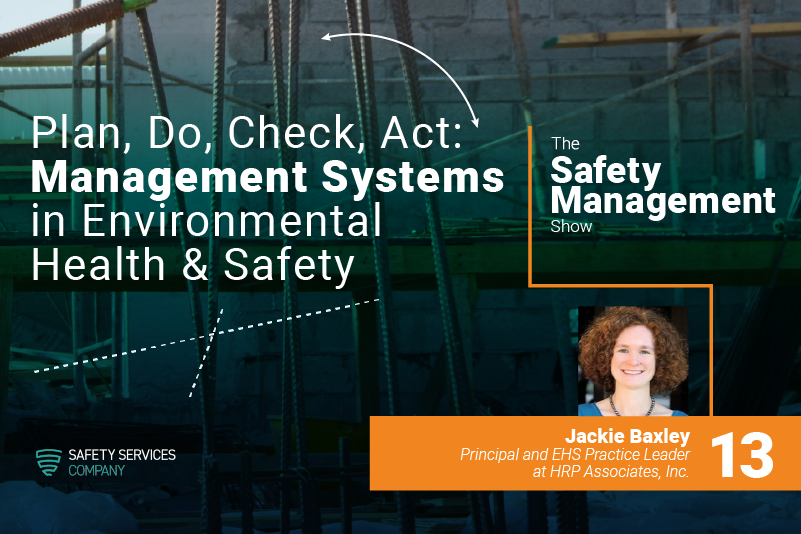
Management systems are a great way to assess and control environmental health and safety issues within your organization. They help you along the implementation journey ensuring you get buy-in at every level.
So how do you go about using a management system?
The framework to remember: plan –> do –> check –> act.
In this episode, Jackie Baxley, Principal and EHS Practice Leader at HRP Associates, Inc., talks about how management systems work and best practices for acquiring certifications.
We discuss:
- Working with clients on COVID programs and protocols
- Management systems, like ISO 14,001 and ISO 45,001
- What makes for a good onboarding system
- Advice for new safety professionals
- Hazard recognition and training
What’s So Important About a Management System?
They help you assess and control quality, and can help you evaluate your occupational health and safety.
“You’ve got to talk and engage with people, you can’t do health and safety from behind a desk.”
— Jackie Baxley
There are international standards for what would be considered a management system. One example of that is ISO 140101, the international standards organization for environmental management systems. Or ISO 45001, the standard for an environmental safety and health management system.
The nice thing about these two standards is that they play very well together. They align with one another, and there’s an awful lot of overlap between the two.
Let’s say you’ve recognized the need for a management system.
What framework should you be following or paying attention to when it comes to implementing those systems?
Plan, Do, Check, Act
As simple as it may sound, a simple framework can be applied to the implementation of a management system. The basic principles of any management system is what’s called “Plan, Do, Check, Act.”
If you take ISO 45001 as your starting point, what would a plan, do, check, act system look like?
You start with PLAN. You start analyzing your hazard assessments, your regulatory obligations, your goals and objectives, and make sure that you get your plan firmly put in place.
Then you DO.
Your plan is in place, now you have to focus on the things that you have to do. What do you need to do in order to meet those certain regulations or requirements that you identified in the PLAN phase? You plan what you need to do, then you develop the tools to do it.
Next is CHECK.
This might seem simple, but all the best plans in the world are useless if they’re not actually working. So you check to make sure you’re on track. Whether it’s internal inspections, monitoring, or reporting, it’s making sure that your plans are working the way they should.
Finally, you ACT.
If after all of the planning, doing, and checking, you find that things aren’t working the way they should, you act to fix it. What went wrong and how can you prevent it from going wrong in the future?
“Exercising that “plan, do, check, act” system will really help you make sure that you’re focusing on what you need to focus on, and that you’re always looking for those opportunities for improvement.”
— Jackie Baxley>
ISO 45001 has a highly prescriptive roadmap, and there are drivers for getting that specific certification. But even if you’re not going for the full certification, just exercising that “plan, do, check, act” mentality will help to make sure that you’re focusing on what you need to focus on, that what you’re doing is working, and that you’re always looking for opportunities for improvement.
Hear more unique stories and insights from safety professionals by subscribing on Spotify. All episodes can be found on our website.